In large and growing companies, supply chain management is the lifeblood of a healthy and efficient business operation. After all, a supply chain encompasses every individual and company in the vast network involved in sourcing the materials for a product until the product is delivered to the customer. With so many different nodes in different places, a supply chain is exposed to a variety of factors. Today, as the world’s economy becomes volatile in unsuspected ways, many managers are shifting their attention to ensuring they have a resilient and sustainable supply chain.
What is Supply Chain Management?
Supply chain management is the management of sourcing raw materials and the processes that eventually transform them into their final product, which are then delivered to the customers. Mainly a business side operation, proper SCM can significantly lower the cost of production, maximize customer value, and give businesses the edge over their competitors. Those who work in this position are typically in charge of inventory, production, distribution, and vendors.
Though there are a multitude of roles in SCM, we can sum the overall steps in supply chain management into 5 steps as follows.
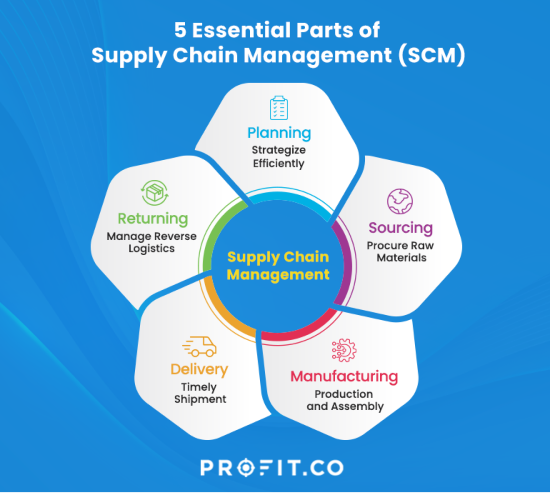
The 5 Essential Parts of SCM
1. Planning
Making sure that supplying the customers closely matches the manufacturing demands. This means making accurate predictions to avoid excess inventory or a shortage.
2. Sourcing
Businesses strive to have a portfolio of diverse and reliable suppliers who can precisely meet their requirements.
3. Manufacturing
It is the process by which raw materials are transformed into the final product through tools, labour, and chemical processing.
4. Delivery
Timely delivery is important in today’s competitive landscape. Effective supply chain management ensures efficient logistics, guaranteeing prompt, quality-driven, and secure deliveries.
5. Returning
In the unfortunate case where a customer needs to return the product, there needs to be a convenient and efficient method for the customer to use, i.e., reverse logistics.
Those who work in SCM are dealing with a lot and need to stay ahead of the game constantly. A way of doing this is by customizing their supply chains according to the specific designs of your product. What would work for a car manufacturer would not work for a clothes manufacturer and we can see this as we discuss the most common supply chains.
The Different Types of Supply Chains
Supply chains come in various models, each one suited for a different purpose. If your business is highly dependent on trends, you would need a supply chain that can quickly change what it manufactures. Alternatively, if your business is old and plans to continue selling the same product for longer, you would need a supply chain that is consistent and reliable.
Perhaps you can recognize your supply chain in the following models:
Continuous flow model
A traditional model is apt for companies that have existed for a long time. You typically just need the same materials to be repeatedly sourced for the same product. Amazon is familiar with this as they have to supply the same products continuously for long periods without interruption.
Agile model
Companies that need to customize their products frequently or have highly varying demands so you need a supply chain that adjusts quickly. H&M, a clothing manufacturer, has to quickly respond to customers’ changing demands; they use this model.
Fast model
Say you’re a fashion company that needs to capitalize quickly on brief trends. In that scenario, you’ll need a supply chain that can support products with quick turnovers and short life cycles. Zara is an excellent example of this, as their speedy delivery is partly what they’re known for.
Flexible model
Similar to the fast model, instead of trends, you respond to changes in the season. Rather than a quick response, you need a supply chain that can significantly increase and then decrease supply as demand changes. Hewlett-Packard has to do so not only to keep up with customers but also with changing software and hardware.
Efficient model
In the case where profit margins are tight, there must be no wastage in the supply chain. All tools, labour, and other resources are used optimally. Toyota, the Japanese multinational automotive manufacturer, puts great emphasis on cutting out waste and unnecessary steps in their production.
Custom model
Perhaps none of the previous models meet your needs, in which case you develop a supply chain unique to your company’s product. Due to the intricacy of assembling their aircraft, Airbus and other major aerospace companies require specialized supply chains. Each part has a different supplier as well as alternatives in the case of a mistake.
Though these models all vary in how they serve the business, they eventually face the same modern problems.
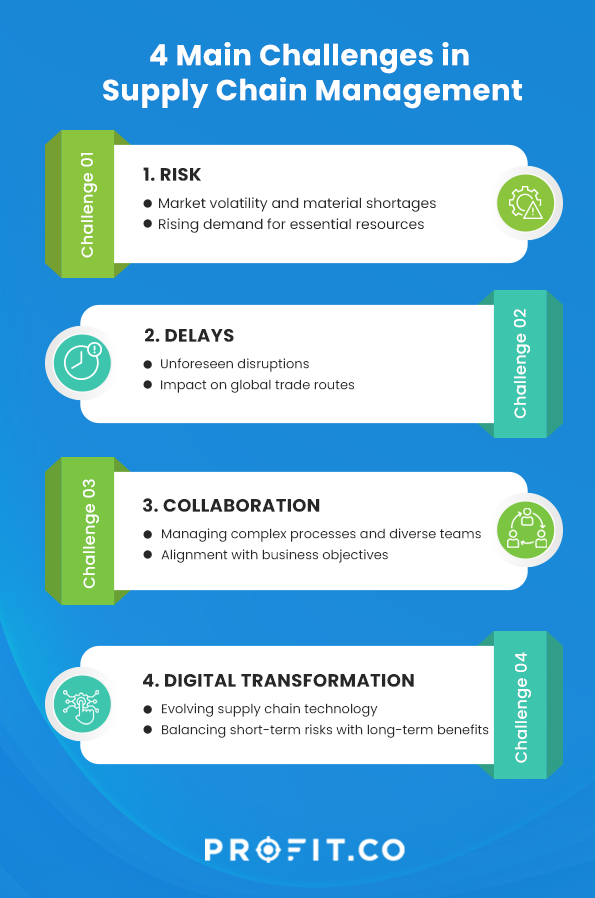
4 Main Challenges in Supply Chain Management
Normally, a manager has to ascertain what are the weak points within the operation they are running and then find ways to improve or remove them. While this is also true for SCM, a lot of their problems are also external. Diversifying a portfolio and being cautious of the vendors you choose are great ways of hedging against risk. Diversification typically means spreading risk by having several alternate suppliers available, especially in the case of essential and rare parts. Still, the market and environment are volatile and there are some things you just can’t prepare for.
1. Risk
Primarily referring to the volatility of the markets today. For example, many companies are striving to find ways to deal with material shortages now. In 2023, one of our most serious concerns is the rising shortage of copper, given how essential it is for wiring and pipes. McKinsey predicts global copper demand will reach 36.6 million tonnes by 2031 due to global electrification.
2. Delays
The most well-planned route and schedule can still be disturbed by factors out of your control. This is particularly well illustrated by the Suez Canal obstruction in March 2021. One of the world’s busiest trade routes, it was blocked by a large container ship. In addition to the difficulty of navigating the canal, the ship faced turbulent environmental conditions as strong winds buffeted them. For six days, other ships could not pass through the passage and we saw trade between Europe, Asia, and the Middle East suffer.
3. Collaboration
The longer your supply chain, the more processes and individuals you need to manage. Aligning everything to your business’s ultimate goal is an arduous process, made more difficult by a lack of shared data, varying methods, and different cultures depending on the size of the operation. In the 1980s, HP’s integrated circuit division chose to carry as little inventory as possible as that was a successful tactic, but this meant long lead times in their supplies to the ink-jet printer division. It ended up with them having greater costs as the ink-jet division simply increased their own inventory of expensive printers to keep up with demand rather than communicate their problem to the integrated circuit division.
“Great things in business are never done by one person, They’re done by a team of people.”
4. Digital transformation
Operating in a supply chain is a continuous process, as trade never stops. Ideally, it would be easier with digital solutions, as most industries are finding out. While in the long run, they would be beneficial, the short-term implementation is a risk many managers would not want to take. The time it would take to install the technology and then train for it could be extremely costly, especially without a well-laid-out methodology. In 2004, LEGO almost became bankrupt due to ineffective digital transformation but made a comeback due to a change in methodology by its new CEO, Jorgen Vig Knudstrop.
These challenges we’ve listed are just some of the variables those working in SCM have to contend with daily. As challenging periods pass, they have to figure out how to maintain and then surpass key performance indicators, as the numbers can be a good measure of their effectiveness.
In cases like this, it’s best to learn from the most successful examples. Google, Amazon, and many large companies have attributed their dominance to their belief in a specific methodology: the OKR methodology. In addition to improving their performance, they also looked to achieve systemic and cultural change, and they found that well-planned and implemented OKRs were extremely effective. First, we should understand how this method came about and then how it can benefit SCM.
A Way to Create Change in SCM
OKR is not just a measure of performance but also a measure of change. Businesses looking to fundamentally improve their operations with specific goals in mind will find great use for this methodology.
The basics of an OKR are
Objective
A straightforward goal to be achieved. They are aspirational and significant. A good objective should prevent vague thinking and will be understood by all members.
Key Results
The benchmarks by which we measure how close we are to achieving the objective. They are measurable, timebound, and aggressive. They give individual members exact ideas on how to progress toward the objective and also indicate when and where they need assistance.
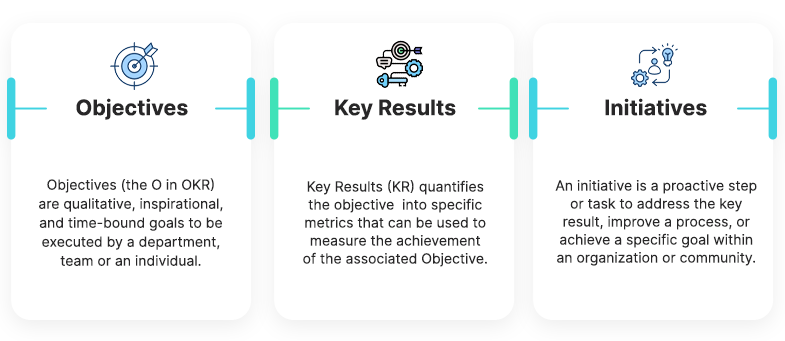
OKRs, or Objectives and Key Results, originated with Andy Grove at Intel in the 1970s, helping the company excel in the competitive microprocessor market. John Doerr, who worked with Grove, introduced OKRs to Google in 1999, contributing to its remarkable success. This goal-setting framework has since been embraced by companies like Amazon, Square, Intuit, and Zynga, spanning various industries. For supply chain managers seeking improvement, adopting OKRs offers a structured approach to enhance efficiency and results, making it a valuable methodology.
To learn more about How OKRs can optimize supply chain operations
Benefits of Reworking Your Supply Chain
Consider the following factors on how a supply chain might benefit from OKRs
Change starts at the top with a focus
The focus of your business and how the supply chain can support that is decided by the executives, and the OKR methodology allows them to share this objective at every level.
Alignment along the supply chain
As the supply chain grows longer, it becomes more difficult to ensure every individual is working towards the same objective. However, the OKR methodology ensures that the top-level executives put in the time to think of transparent and clear objectives. Each team is prompted to think of their OKRs that can help them contribute to completing the company’s Objective.
Pushes individuals to work outside their comfort zone
A key aspect of an OKR is being aspirational. You want employees to go beyond “business as usual” and be creative. That is the “stretching” aspect of OKRs is what prompts this.
Increases passion and commitment to tasks
When an employee feels aligned with their organization and is able to contribute directly to its goals, it gives them a sense of purpose and identity tied to the organization. Hence, we see an increased commitment by them to push their limits and achieve greater results.
A tool for tracking progress
OKRs are excellent ways of evaluating new changes. This methodology only works with consistent check-ins and reviews are followed in case an early change in course is required. Given supply chain managers are hesitant to implement major technological change, using OKRs can give them an idea of where change can be most easily implemented and which individuals are committed to it.
OKRs are typically tracked on a quarterly basis, with a crucial emphasis on regular review and clear grading methods, such as Google’s percentage scale from 0.0 to 1.0, to assess objective achievement.
But how can this be implemented in your SCM?
Implementing Change in Your Supply Chain
Like any good strategy, implementation relies on the people involved. Therefore, the following points are things to keep in mind.
1. Understand the company goals
Context matters. Consider your company has survived the worst parts of the COVID-19 pandemic. You have weathered increased regulations in transport and greater employee turnover. You are now aiming to recover.
2. Facilitate team discussion for Objectives
The goal is “change” throughout the company, which means you need a multi-faceted perspective. Form your team and develop aspirational objectives that everyone can get behind. Let us choose an example of an “Objective: Increase customer satisfaction.”
3. Debate and select Key Results:
With several people brainstorming, you can consider key results that will help accomplish the objective you desire. Ultimately, you only need 3-5 key results.
Objective: Increase customer satisfaction.
KR 1: Increase on-time delivery by 20%
KR 2: Reduce late deliveries by 10%
KR 3: Reduce returns by 30%
4. Communicate to all levels of the organization
Your final OKR is not a private choice. Ensure everyone in the organization knows, and then encourage employees to contribute their ideas on achieving these OKRs. The customer service department will have their ideas to reduce returns as they are the most experienced. Similarly, other departments will be able to contribute in their own unique ways.
What to Avoid?
The most important point to remember is that this does not happen instantly. OKRs are not typically created and deployed in a few hours. Take your time to understand what the business needs now and think it over. And then provide space for reviews and feedback in your timeline. Though a quarter is a typical time frame, it can vary depending on what you have set as your OKR. Change in SCM takes place over a long time frame and it’s important the planning reflects that as well.
Additionally, OKRs should not be tied to compensation. That is what KPIs are typically used for. You want to inspire employees to be more creative and try new things that can be greatly hampered if they fear their pay depends on it.
Conclusion
In wrapping up, it’s evident that the complexities and unforeseen challenges in Supply Chain Management require innovative solutions, and this is where the strength of OKRs truly comes to the fore. These objectives and key results not only offer a structured way to set and monitor goals but also encourage agility and adaptability. In an era where economic disruptions are frequent and global crises can reshape industries overnight, introspection becomes crucial. Organizations need to delve deep, assessing their internal processes, strategies, and goals. It’s about more than just navigating challenges; it’s about thriving amidst them. The OKR methodology, with its focus on clarity, alignment, and measurable outcomes, stands out as a beacon for businesses looking to not just survive but excel in today’s volatile marketplace.